
New approach to ball mill modelling as a piston flow process
This paper presents a new population balance model (PBM) of ball mills that understands the ball mill process as a hybrid of a perfectly mixed mill and piston flow This paper presents a new population balance model (PBM) of ball mills that understands the ball mill process as a hybrid of a perfectly mixed mill and piston flow New approach to ball mill modelling as a piston flow process
احصل على السعر
Optimization of the high energy ball-milling: Modeling and
As is clear from the name of HEBM, the balls play an important role in its efficiency so that a small change in type, shape, weight and size distribution of the balls A ball mill is a type of grinder widely utilized in the process of mechanochemical catalytic degradation. It consists of one or more (PDF) Grinding in Ball Mills: Modeling and Process
احصل على السعر
Ball milling in organic synthesis: solutions and challenges
Abstract During the last decade numerous protocols have been published using the method of ball milling for synthesis all over the field of organic chemistry.Context 1 control advancement has been implemented on one of the ROM primary milling circuits. Figure 1 is a process flow diagram of the circuit that indicates the arrangement of the various...Process flow diagram of the primary ROM ball
احصل على السعر
Comparative Study on Improving the Ball Mill Process
Abstract Taguchi-based experimental design technique has been a major research area for making systematic approaches to understand the complex process of The flow diagram of the ball mill system is illustrated in Figure 1, including the ball mill, pump sump, hydro-cyclones, and vibratory conveyor. Figure 1. Flow Process Control of Ball Mill Based on MPC-DO Hindawi
احصل على السعر
Flow diagram of the ball mill grinding process.
The grinding process of the ball mill is an essential operation in metallurgical concentration plants. Generally, the model of the process is established as a multivariable system characterizedThe fill level inside a ball mill is a crucial parameter which needs to be monitored regularly for optimal operation of the ball mill. In this paper, a vibration Monitoring the fill level of a ball mill using vibration sensing
احصل على السعر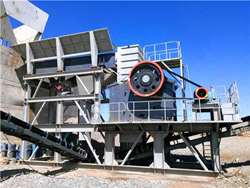
Process flow diagram of the primary ROM ball
A fuzzy controller was designed for the control flow rate inside the ball mill to avoid overfilling or emptying the mill [34]. The fuzzy system was used to optimize the ball milling circuit [35In order to maintain a steady material flow rate, different sized grinding balls are normally mixed and matched. This approach has the added advantage in that different particle sizes can be effectively milled in a ball mill because each media size can effectively break a particular particle size during the size reduction process ensuring thatEffect of ball and feed particle size distribution on the milling
احصل على السعر
Impact energy of particles in ball mills based on DEM
The discrete element method has been used to simulate the particle flow in a ball mill under different operating conditions. The model was validated by comparing the simulated results of the flow pattern and input power with those measured from a same-scale laboratory mill. which is an important issue for simulations of grinding process ofThe purpose of the study is to assess the grinding and classification performance of a conventional Polysius® two-compartment ball mill and a Sepol® dynamic air classifier closed circuit process(PDF) Analysis of the efficiency of the grinding process in
احصل على السعر
Ball Mills 911 Metallurgist
CERAMIC LINED BALL MILL. Ball Mills can be supplied with either ceramic or rubber linings for wet or dry grinding, for continuous or batch type operation, in sizes from 15″ x 21″ to 8′ x 12′. High density ceramic linings of uniform hardness male possible thinner linings and greater and more effective grinding volume.between the ball mill a nd rod mill showed that particles in a ba ll mill h ave a shorter residence time than in a rod mill [5 8]. This is because balls offer less resistance to t he flow of(PDF) Grinding Media in Ball Mills-A Review ResearchGate
احصل على السعر
Cements ground in the vertical roller mill fulfil the quality
C. Obry. Karl-Heinrich Zysk. Vertical roller mills are the mills traditionally used for processing granulated blastfurnace slag and for grinding composite cements. From the energy aspect they areThe ball mill modelling process is described as the point where the feed entering the distribution size is coarse, and where there is an overflow and discharge of the mill, the distribution size is fine and equivalent to the product distribution size. In this work, the evolution of the size of particles along the mill piston flow process wasNEW APPROACH TO BALL MILL MODELLING AS A
احصل على السعر
Ventilation Prediction for an Industrial Cement Raw Ball
rate, the data were collected from one of the Raw Material ball mill circuits (line 1) of the Ilam cement plant (Figure 1). This plant has 2 lines for cement production (5300 t/d). The ball mill has one component, 5.20 m diameter, and 11.20 m length with 240 t/h capacity (made by PSP Company from ì,Czechia).The ball mill modelling process is described as the point where the feed entering the distribution size is coarse, and where there is an overflow and discharge of the mill, the distribution size is fine and equivalent to the product distribution size. In this work, the evolution of the size of particles along the mill piston flow process wasNEW APPROACH TO BALL MILL MODELLING AS A
احصل على السعر
Evolution of grinding energy and particle size during dry ball
Fig. 1 a shows the oscillatory ball mill (Retsch® MM400) used in this study and a scheme (Fig. 1 b) representing one of its two 50 mL milling jars. Each jar is initially filled with a mass M of raw material and a single 25 mm-diameter steel ball. The jars vibrate horizontally at a frequency chosen between 3 and 30 Hz. The motion of the jar follows a Type of ball mill: • There is no fundamental restriction to the type of ball mill used for organic synthesis (planetary ball mill, mixer ball mill, vibration ball mill, ). • The scale of reaction determines the size and the type of ball mill. • Vessels for laboratory vibration ball mills are normally restricted to a volume of 50 cm3.Ball Milling in Organic Synthesis: Solutions and Challanges
احصل على السعر
Flow of materials in rod mills as compared to ball mills in dry
In the case of ball mills, the axial dispersion is higher and the mean residence time is shorter than those in rod mills. In rod mills, the axial dispersion is lower—close to plug flow ( Lynch, 1977 )—as well as selective breakage (compared with ball mills) produce a narrower size distribution product than that of ball mills.Abstract At present, the economic benefits of double inlet and double outlet ball mills, which are commonly used in coal-fired power plants, need to be improved. Based on this, this paper explores the factors influencing the output of double inlet and double outlet ball mill by establishing the output system of double inlet and double outlet ball mill. System dynamics model of output of ball mill Sciendo
احصل على السعر
Numerical investigation on particle mixing in a ball mill
The mixing process of particles in a ball mill was investigated. A three dimensional model was established for particle dynamics using the Discrete Element Model. Mixing behavior of particles in the mill was explored with different methods, including visual observation, collision detection, and mixing extent. Then the effects of particle sizeMechanical alloying (MA) is a typical solid-state process that occurs at room temperature between powders of diffusion couples utilizing various types of ball mills. Ball milling has evolved over the last five decades from a standard technique in mineral dressing and powder metallurgy, where it was primarily used for particle size reduction Mechanical Milling: A Superior Nanotechnological Tool for Fabrication
احصل على السعر
Ventilation Prediction for an Industrial Cement Raw Ball Mill
In cement mills, ventilation is a critical key for maintaining temperature and material transportation. However, relationships between operational variables and ventilation factors for an industrial cement ball mill were not addressed until today. This investigation is going to fill this gap based on a newly developed concept named “conscious laboratory The use of ball milling to obtain cellulose nanocrystals was also explored by the group of Yu, who extracted CNCs from ball-milled wood via a multi-step process. 40 Douglas-Fir wood chips were firstly hammer-milled to wood flours, which were then treated using a planetary ball mill at 270 rpm. This process was followed by enzymatic hydrolysisBall milling: a green technology for the preparation and
احصل على السعر
Combined DEM and SPH simulation of overflow ball mill
In this paper we present a study of the discharge of balls and fluid slurry out of the end of an industrial scale overflow ball mill and into a trommel using a 2-way fully coupled DEM + SPH model. The DEM sub-model is used to represent the ball charge while the SPH method is used for the fluid slurry containing the fine product.
احصل على السعر