
Life cycle assessment of iron ore mining and processing
As loading and hauling followed by crushing and screening are the two main stages contributing to the energy and GHG footprints of iron ore mining and processing, Making iron and steel from iron ore requires a long process of mining, crushing, separating, concentrating, mixing, agglomeration (sintering and pelletizing), Iron Ore Processing, General SpringerLink
احصل على السعر
Iron processing Ores, Smelting, Refining Britannica
Iron processing Ores, Smelting, Refining: Iron ores occur in igneous, metamorphic (transformed), or sedimentary rocks in a variety of geologic environments. Most are The iron ore processing industry produces usable concentrations of iron-bearing material by removing nonferrous rock (gangue) from low-grade ore. In the United Iron Ore Processing, General Springer
احصل على السعر
(PDF) Life cycle assessment of iron ore mining and
Life cycle assessments of the mining and mineral processing of iron ore, bauxite and copper concentrate were carried out, focussing on embodied energy and greenhouse gas emissions.Modern sintering process consists of three stages: sintering raw material preparation, sintering, and sinter processing (Fig. 1). Sintering raw material preparation Iron Ore Sintering SpringerLink
احصل على السعر
(PDF) Effective Processing of the Iron Ores
The urgent task of improving the quality of iron ore concentrates was studied. We propose to use the stage-wise removal of the concentrate by combining fine screening, regrinding, and magneticAbstract. Mining of iron ore is a highly capital- and energy-intensive process. Life cycle assessment (LCA) of the mining and mineral processing of iron ore in Australia was carried out in this chapter using SimaPro LCA software as a case study. The environmental impacts considered in the study were embodied energy and greenhouse Life cycle assessment of iron ore mining and processing
احصل على السعر
Iron ore beneficiation: an overview ScienceDirect
Dry processing of iron ore: In dry processing of iron ore, ROM is generally crushed below 40 mm through three-stage crushing and thus segregated by screening into 10–40 and −10 mm fractions. For softer ore, tumbler index is generally low and hence lump ore is crushed below 10 mm to produce 100% fine product. Yield from the plants has Transforming iron ore processing Simplifying the comminution and replacing reverse flotation with magnetic and gravity separation Interestingly, the two-stage process appears to be equivalent to the single stage separation achieved using the Reflux Classifier, with a combined recovery of 0.889x93.4 ∼ 83%, and a similar Fe grade Transforming iron ore processing ScienceDirect
احصل على السعر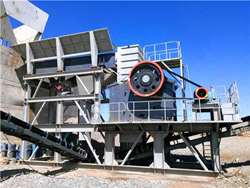
Induration Process of Pellets Prepared from Mixed Magnetite J-STAGE
The induration process for green pellets involves 4 main stages: (1) drying, (2) preheating, (3) heating and (4) cooling. In the drying stage (105–260°C), water is removed from the pellet in a controlled process to avoid cracking. During preheating (260–845°C), oxidation of the magnetite and decomposition of carbonates occur.several stages of refining or other purification processes may be employed. Table10.1. Common Forms of Metal Minerals Metal Mineral Mineral Name Aluminum Al 2O The transformation of iron ore into steel products. (a) Processing of iron ore. (b) Manufacture of steel ingots. The most common are stainless steels, with several Metal Ore Extraction and Processing Springer
احصل على السعر
Introduction: Overview of the global iron ore industry
Turning to iron ore exports and imports, the tonnages are summarized in Table 1.1 for 2012 and 2018 (Australian Department of Industry, Science, Energy and Resources, 2021; US Geological Survey, 2020; United National Conference on Trade and Development (UNCTAD), 2021).As shown in Fig. 1.3, China is the largest iron ore The loss of beneficiation and iron-making of domestic iron ore accounts for more than 80% of the total loss. In 2018, China invested 922 million tons of iron ore at the iron and steel production stage, including 660 million tons of imported iron ore, and it lost 169 million tons of iron in the iron and steel production process.Analysis of iron composite flow in China SpringerLink
احصل على السعر
[GIFS] The 5 Stages of the Mining Life Cycle Mining Digital
The first step in the production stage is recovering the minerals. This is the process of extracting the ore from rock using a variety of tools and machinery. The second step is processing. The recovered minerals are processed through huge crushers or mills to separate commercially valuable minerals from their ores.Transforming iron ore processing Simplifying the comminution and replacing reverse flotation with magnetic and gravity separation Such dilution of the ore fed to the plant has demanded the inclusion of grinding stages to liberate the valuable iron oxides from the gangue, typically to sizes below about 0.15 mm (França et al., 2020Comminution and liberation response of iron ore types in a
احصل على السعر
Metals Free Full-Text Non-Isothermal Reduction
This study investigates the non-isothermal reduction of iron ore fines with two different carbon-bearing materials using the thermogravimetric technique. The iron ore fines/carbon composites were the Chengchao iron ore miner, Ezhou, Hubei, China. The raw iron ore powder was rst calcined at 900 C for 6 h under atmospheric air. Then, the iron ore was grinded and sieved to 60–250 mm for use. The chemical components of the calcined iron ore were determined by X-ray uorescence (XRF) spec-troscopy. The results are given in Table 1.Chemical looping hydrogen production with modified
احصل على السعر
A review on the characterisation and processing of oolitic iron ores
Excellent results were claimed in processing 300 t of ore in a pilot plant at 1 tph. Gravity processing Lorraine oolitic limonite ores using spirals in the size range 0.1–0.5 mm produced a concentrate containing 40–42% Fe, 12–15% SiO 2, 4–5% CaO and 6% Al 2 O 3 at an iron recovery of 65% ( Durand et al. (1965) ).The iron (Fe) content of such ores ranges from 72% to 35%. The highly friable and fully liberated constituents in ore, such as alumina and silica, generate a large quantity of fines during mechanized mining and crushing. Fine gangue material or iron ore slimes having <45%–55% Fe are discarded as reject during the ore beneficiation process.Iron ore slimes beneficiation using optimised ScienceDirect
احصل على السعر
Process through Multiscale Process Modeling mdpi
wustite stage, the pores enlarge and the wustite grains break down into smaller particles termed “crystallites”. These subsequently grow (typically from 1 to 10 m) and join to form the molten-like (Figure2) is the core of the DR process. Iron ore pellets are charged at the top, descend due to gravity, and encounter an upward counterThere is a constant risk of iron ore collapsing during its transfer between processing stages in beneficiation plants. Existing instrumentation is not only expensive but also complex and challenging to maintain. In this research, we propose using edge artificial intelligence for early detection of landslide risk based on images of iron oreDeep Learning Approach at the Edge to Detect Iron Ore Type
احصل على السعر
Hydrogen Plasma Processing of Iron Ore SpringerLink
Iron is currently produced by carbothermic reduction of oxide ores. This is a multiple-stage process that requires large-scale equipment and high capital investment, and produces large amounts of CO2. An alternative to carbothermic reduction is reduction using a hydrogen plasma, which comprises vibrationally excited molecular, atomic, and exploitation to an environmentally deleterious process. Table 2. CO 2 emissions in ore mining and processing 2.2 Influence of reducibility The effects of selecting an appropriate iron ore are relevant when the ore is reduced in a blast furnace. Although hematite possesses a higher ratio of oxygen (O/Fe = 1.5) than does magnetite (O/Fe = Redalyc.NATURAL RESOURCES SUSTAINABILITY: IRON
احصل على السعر
Kinetics of Reduction in Stages of Pellets Prepared from the
To explore the reduction swelling process of pellets prepared from the Bayan Obo iron ore concentrate, based on the iron oxide reduction theory of pellets, the reduction of pellets prepared from the Bayan Obo iron ore concentrate was analyzed by thermogravimetric experiments and kinetic calculations in three stages. The reason for 10.1. Physical processing for enhanced chemical and/or physical properties. Hematitic/goethitic iron ore as a bulk commodity is normally treated at its source (mine) through relatively simple physical ore dressing processes of comparatively large scale to turn it into salable products prior to transportation. The overall purpose of such treatment Developments in nonmagnetic physical separation technologies for
احصل على السعر