
Recommended Ball Mill Speed & Liner
Mill critical speed is defined as that rotational speed at which an infinitely small particle will centrifuge, assuming no slippage C.S. = 76.63 / 11^0.5 = 23.1 rpm Ball and SAG Mills are driven in practice at a speed corresponding to 60-81% of the critical speed, the choice of speed being Ball Mill Critical Speed 911 Metallurgist
احصل على السعر
Critical rotation speed for ball-milling ScienceDirect
Critical rotation speed of dry ball-mill was studied by experiments and by numerical simulation using Discrete Element Method (DEM). The results carried out by Each mill is designed by fixing a rotational-to-revolution speed ratio [ r] ( r=Np / Nr, [ Np] is rotation speed of the pot and [ Nr] is revolution speed of the disk). Optimum revolution and rotational directions and their speeds
احصل على السعر
Ball Mill an overview ScienceDirect Topics
The company clams this new ball mill will be helpful to enable extreme high-energy ball milling at rotational speed reaches to 1100 rpm. This allows the new mill to achieve At a low mill rotational speed, Soni and Mishra perceived that bigger balls move near the periphery of the mill and smaller balls clutter around the kidney of the A Review of the Grinding Media in Ball Mills for Mineral
احصل على السعر
Machines Free Full-Text Modeling Impulsive Ball Mill
The mill speed is defined as the percentage of the critical speed C s. The critical speed C s of the mill is the rotation speed at which the balls are subject to Mio et al. (2004) determined the critical rotation-to-revolution speed of vials and sun using the planetary ball mill for the effective grinding of the gibbsite powder Optimum revolution and rotational directions and their
احصل على السعر
Mill Speed an overview ScienceDirect Topics
Ball and Race Mill (Figure 4.10): In the ball-and-race mill, balls are held between two races, much like a large ball bearing. The top race or grinding ring remains stationary while the The rotational direction of a pot in a planetary ball mill and its speed ratio against revolution of a disk were studied in terms of their effects on the specific impact Effects of rotational direction and rotation-to-revolution speed
احصل على السعر
Ball milling: a green technology for the
The ball mill Ball milling is a . 70 This nanocomposite was obtained by mixing commercially available CNCs with UHMWPE in a planetary ball mill at 200 rpm rotational speed for six hours. The resulting mixture was then The rotational direction of a pot in a planetary ball mill and its speed ratio against revolution of a disk were studied in terms of their effects on the specific impact energy of balls calculatedEffects of rotational direction and rotation-to-revolution speed
احصل على السعر
Ball Mill an overview ScienceDirect Topics
Conical Ball Mills differ in mill body construction, which is composed of two cones and a short cylindrical part located between them The company clams this new ball mill will be helpful to enable extreme high-energy ball milling at rotational speed reaches to 1100 rpm. This allows the new mill to achieve sensational centrifugaldepending on feed size and mill speed. The parameters and were constant at 7.3 and 1.17 respectively. Key terms: Population balance Model, ball milling, communition, Size specific energy, Selection function, breakage function, mill critical speed, Platinum ore, milling kinetics, breakage rate.EFFECTS OF MILL ROTATIONAL SPEED ON THE BATCH
احصل على السعر
Kinetic Energy Dose as a Unified Metric for Comparing Ball Mills
A planetary ball mill (Pulverisette seven premium line, Fritsch) equipped with stainless steel milling jars (80 ml filling capacity) and stainless steel balls were used. An experimental set was generated by varying rotational The mill speed is defined as the percentage of the critical speed C s. The critical speed C s of the mill is the rotation speed at which the balls are subject to centrifugal force while adhering to the inner surface of the drum [4,24,25]. It can be calculated by the following Equation (1).Machines Free Full-Text Modeling Impulsive Ball Mill
احصل على السعر
Effect of grinding media on the milling efficiency of a ball mill
The size of grinding media is the primary factor that affects the overall milling efficiency of a ball mill (e.g. power consumption and particle size breakage). This article tackles the lack of aThe calculation [8-10] reveals that when D (size of steel ball) = 25 mm and n (rotation speed of mill) ≤ 12.34 rpm, the steel balls inside the mill attain the state of cascading, and the reduction in particle size is induced by the abrasion action. Low-speed grinding tests are performed for pyrite and quartz at three different feed sizes (-3.Journal of Physics: Conference Series IOPscience
احصل على السعر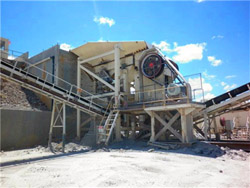
Materials Free Full-Text Effect of Different Rotational
The rotational speed of the ball mill is adjusted to 200, 240, and 280 rpm, and the above steps repeated for the experiment. 2.3. Experimental Equipment. Graphene-wrapped SiC core-shell nanoparticles were synthesized using a planetary ball mill (Retsch PM100, Verder Group, Haan, Germany) at 220 V voltage and 16 A current in one step. ball mill types like mixer mills or stirred media mills are for instance the simple set up, the good cleanability and moderate The high rotational speed of both, the pots and the disk, leadsChem Soc Rev ResearchGate
احصل على السعر
Minerals Free Full-Text Rod Mill Product Control
The rotation speed of the drum (expressed as a percentage of a certain critical speed, Vc) also affects breakage kinetics. This percentage of the critical rotational speed on tumbling mills normally The ball mill Ball milling is a . 70 This nanocomposite was obtained by mixing commercially available CNCs with UHMWPE in a planetary ball mill at 200 rpm rotational speed for six hours. The resulting mixture was then hot-pressed to form disk-like or dumbbell shaped derivatives, which had an improved biocompatibility and could therefore beBall milling: a green technology for the preparation and
احصل على السعر
(PDF) EXPERIMENTAL STUDY OF THE EFFECT OF BALL
It is also found that 1500 RPM of rotational speed with 16 mm ball diameter and 222 g rotating mass is the optimum condition to reach minimum milling time and minimum output grain size. UnbalanceIn recent research done by AmanNejad and Barani [93] using DEM to investigate the effect of ball size distribution on ball milling, charging the mill speed with 40% small balls and 60% big balls(PDF) Effects of Ball Size Distribution and Mill Speed and
احصل على السعر
(PDF) Vibration characteristics of an operating ball mill
In the range of rotational speed before the grinding rate falls, the grinding rate is improved when grinding with balls of 12.7 mm or less, while it is reduced when larger balls over 15.9 mm are used.where R = radius of ball mill; r = radius of ball. For R = 1000 mm and r = 50 mm, n c = 30.7 rpm. But the mill is operated at a speed of 15 rpm. Therefore, the mill is operated at 100 x 15/30.7 = 48.86 % of critical speed. If 100 mm dia balls are replaced by 50 mm dia balls, and the other conditions are remaining the same,Ball Mill Operating Speed MSubbu Academy
احصل على السعر
PAPER OPEN ACCESS Effect of Lifter Shapes on the Mill
The simulations were operated at 30% ball filling for six levels of mill speed (N=50%, 60%, 70%, 80%, 90%, 100% of critical speed). Figure 1. DEM model A method of charge position density limit was used to predict the charge behaviour. In the cross section of ball mill, it was meshed into 100×100 cells, which represents the number of particlesIf the rotational speed exceeds this limit, the centrifugal force surpasses the gravitational force, and balls will keep rotating in the inner periphery of the chamber [16], [21]. The common type of tumbling ball mill used is the bond ball mill. The small-scale mill is 30 cm in diameter and 30 cm in length.Ball-milling: A sustainable and green approach for starch
احصل على السعر
Frequency domain characterization of torque in tumbling ball mills
Ball mills have a low efficiency rate partially due to the lack of a proper method to monitor the mill filling level, which makes it difficult to control the grinding process. (LTH) is expected to appear at frequency nw, n being the number of lifters inside the mill and w the rotation speed expressed in Hz. This LTH can be clearly
احصل على السعر