
Research of iron ore grinding in a vertical-roller-mill
One reason is the dry in-bed grinding principle. Results of extensive test works with two types of magnetite iron ores in a Loesche VRM are presented here. Background The vertical mill was invented in Japan in the 1950s by the Tower Mill Kubota Corporation for applications in fine and ultrafine grinding and was the Vertical mill simulation applied to iron ores ScienceDirect
احصل على السعر
Different Effects of Wet and Dry Grinding on the Activation of Iron Ore
The effect of wet grinding on the activation of IOTs was evaluated through ion leaching from an alkaline solution and the reactivity index. Additionally, a detailed comparison between The grinding parts of a Loesche mill ( Fig. 1) are a rotating table (1) with a horizontal grinding track and rollers (2), which are pressed onto the table by lever arms Research of iron ore grinding in a vertical-roller-mill
احصل على السعر
Investigation on Iron Ore Grinding based on Particle Size Distribution
In the iron and steel industry, the production of narrow particle size distribution (PSD) for pellet feed making with acceptable liberation of valuables from the This paper brings together two separate studies, in which the vertical roller mill was used to grind two different precious metal ores, an epithermal gold deposit (PDF) LEARNING FROM OTHER INDUSTRIES; WHY THE VRM
احصل على السعر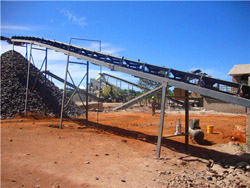
Operational parameters affecting the vertical roller mill
Grinding test results for zinc ore showed that it is possible to decrease the total grinding energy consumption from 20.11 to 11.40 kW h/t by using vertical roller mill Request PDF On Mar 15, 2015, Mathis Reichert and others published Research of iron ore grinding in a vertical-roller-mill Find, read and cite all the research you need on Research of iron ore grinding in a vertical-roller-mill
احصل على السعر
Investigation on the particle size and shape of iron ore pellet
An effect of a grinding method, that is ball mill and high pressure grinding rolls (HPGR), on the particle size, specific surface area and particle shape of an iron ore concentrate was studied. The particle size distribution was meticulously examined by In this study, the relationship between acoustic emissions and hardness of different rock types (model quartz, model calcite, and real iron ore) coupled with binary mix ratios of model quartz and iron ore (1:3, 1:1 and 3:1) was investigated in a laboratory-based AG/SAG mill. The acoustic emission response and sensitivity of the mill wereFeed hardness and acoustic emissions of autogenous/semi
احصل على السعر
Iron ore beneficiation: an overview ScienceDirect
Dry processing of iron ore: In dry processing of iron ore, ROM is generally crushed below 40 mm through three-stage crushing and thus segregated by screening into 10–40 and −10 mm fractions. For softer ore, tumbler index is generally low and hence lump ore is crushed below 10 mm to produce 100% fine product. Yield from the plants has DOI: 10.32604/jrm.2021.015793. ARTICLE. Different Effects of Wet and Dry Grinding on the Activation of Iron Ore Tailings. Yingchun Yang 1, *, Liqing Chen 1 and Yuguang Mao 2. 1 College of Engineering, Anhui Agricultural University, Hefei, 230036, China 2 College of Civil Engineering, Hunan University, Changsha, 410082, China * Corresponding Author: Different Effects of Wet and Dry Grinding on the Activation of Iron Ore
احصل على السعر
Chinese Company Carries Out First Shipment of Iron Ores
These products are from a 1.5 million tonnes/year dry grinding mill at the Bong mine in central Liberia. The Liberian government was expected to grant a 25-year “A-level” iron ore mining licence to the China’s Baowu Group-backed Bao Chico Resources Liberia Company, after it has asked the Government of Liberia to grant it a 25-year Class Figure 1 Definition of Mill Diameter D, Mill Length L, and Effective Grinding Length EGL An exa mple wo uld be a 40’ x 29’ (26’ EGL) [12.19 m x 8.84 m] (7.92 m EGL) 28 M W S AG(PDF) Autogenous and Semi-Autogenous Mills, 2015 Update
احصل على السعر
Application of model predictive control in ball mill grinding circuit
Model predictive control has been employed to handle the strong coupling multivariable system of grinding circuit. A four-input–four-output model of grinding circuit has been developed for process control. Constrained model predictive control has been evaluated in an iron ore concentrator plant. Compared with the former two-input–two Comparison of dry and wet grinding process in an electromagnetic mill is presented in this paper. The research was conducted in a batch copper ore grinding. Batch mode allows for precise parametrization and constant repetitive conditions of the experiments. The following key aspects were tested: processing time, feed size, size of Comparison of Wet and Dry Grinding in Electromagnetic Mill
احصل على السعر
TON to supply two grinding mills to iron ore producer in
A Canadian iron ore producer has awarded TON an order for two powerful Vertimill ® 4500 grinding mills to be delivered in 3Q24. The value of the order, which exceeds €10 million, has been booked in Minerals segment’s 2023 third-quarter orders received. Graham Davey, Director, Stirred Mills at TON, comments: “We are A considerable amount of test work has been carried out by WEIR Minerals covering dry grinding flow sheets, and further test work is in progress. The moisture content of pre-grinding of fine iron ores, near 3–5%, could very well be handled and obviously would reflect the ore moisture as supplied to a plant.Pellet feed grinding by HPGR ScienceDirect
احصل على السعر
Why is vertical roller mill-based dry grinding not used in iron ore
Vertical roller mills (VRM) are commonly used in the processing of iron ore for dry grinding for several reasons: vertical roller mill Energy Efficiency: VRMs are known for their energy efficiency.The energy consumption of the total grinding plant can be reduced by 20–30 % for cement clinker and 30–40 % for other raw materials. The overall grinding circuit efficiency and stability are Energy-Efficient Technologies in Cement Grinding
احصل على السعر
Developments in iron ore comminution and classification
Iron ore grinding and classification. Compared to direct shipping hematite ores mined from the upper regolith, magnetite deposits are much finer-grained and therefore require significant grinding to liberate the magnetite from its silicate matrix. In general, ball mills can be operated either wet or dry and are capable of producing productsDry grinding has been utilised in the cement industry for many years for comminution of limestone, slag and clinker, firstly through ball and rod mills, and in recent decades using high pressure(PDF) Case Study of Dry HPGR Grinding and Classification in Ore Processing
احصل على السعر
What Role does the Grinding Machine Play in Iron LinkedIn
Grinding liberates valuable iron ore minerals from gangue minerals, making it easier to separate and recover the iron content. Ball mill is widely used in iron ore beneficiation plants for dryBall mills are used for wet grinding iron ore, g old/copper ore, nickel ore and other ores, In wet and dry flue gas cleaning processes, sodium compounds are used in the power industry(PDF) SIZE REDUCTION BY GRINDING METHODS
احصل على السعر
Characterization and Beneficiation of Dry Iron Ore Springer
Iron ore is the basic raw material for iron and steel making. India is among the leading producers of iron ore in the world and produces about 150 million tons per annum (U. S. []).The total reserves of iron ore in India is around 28.5 billion tons, of this hematite ore is considered to be the most important iron ore because of its high grade 2. Iron ore screening process: Iron ore screening equipment generally uses a circular vibrating screen to screen the materials after the second crushing. Generally, materials with a size of 10mm or less can be screened for dry selection. After screening, materials with a size of 10-40mm enter the fine crusher for fine crushing.Iron ore crushing and screening process TY Ultrafine
احصل على السعر
Friction and wear of liner and grinding ball in iron ore ball mill
To understand the friction and wear of working mediums in iron ore ball mills, experiments were conducted using the ball cratering method under dry and wet milling conditions, which mimic the operating conditions in ball mills. The liner sample is made of Mn16 steel, the ball had a diameter of 25 mm and was made of GCr15 steel, and the iron The importance of comminution test works originates from the high level of energy consumed in the processing chain to grind the ore to achieve a desirable particle size, liberation, and high iron(PDF) Processing of Magnetite Iron Ores–Comparing Grinding Options
احصل على السعر