
Iron Ore Pelletizing Process: An Overview
Bentonite, an inorganic binder, has been the main binder used in the iron ore pelletizing process since the beginning of pellet This chapter aims to provide an overview and the evolution of iron ore pelletizing process including: Pelletizing process and raw materials Balling technologies Iron Ore Pelletizing Process: An Overview IntechOpen
احصل على السعر
Iron ore pellet plant Manufacturers & Suppliers, China iron ore pellet
Contact Now. US$ 250000 / Piece. 1 Piece (MOQ) Mining Equipment Mineral Machinery Mining Machinery Cement Plant Cement Machinery Ball Mill kiln Cement Mill wood pellet PDF In the last years, pelletizing has been playing an important role in iron ore mining and in iron production (iron making and direct reduction). Find, read and cite all the research youTHE GROWING IMPORTANCE OF PELLETIZING
احصل على السعر
Iron Ore Pelletization Technology and its Environmental
The plant used iron ore concentrate as input and produced superior iron ore pellets for blast furnace and direct reduced iron feed. Since then, Grate-Kiln Systems Iron ore pellet making process involves balling of green mix (containing iron ore fines, binder, limestone and coke) using rotating disk or drum to produce green pellets.(PDF) Iron Ore Pelletizing Process: An Overview
احصل على السعر
Traveling Grate Pelletizing Plant TON
Get uniform pellets with excellent metallurgical and physical properties. TON's traveling grate pelletizing plant is the industry's leading induration technology for iron ore pellet 15.1. Introduction Iron ore lump, sinter, and pellets comprise the main burden of modern blast furnaces. However, sinter and pellets are now the dominant blast Iron ore pelletization ScienceDirect
احصل على السعر
OPTIMIZATION OF IRON ORE PELLETS PRODUCTION IN
Then the iron ore pellets will sent through metallic conveyor into the furnace to undergo heating process at 1200 degrees. After the heating process, the heated base mix will converted into a semi liquid cake. Using a sinter breaker machine the cake is break into small pellets. Finally these iron ore pellets under goes cooling in the cooling Indian iron ores are suffering from high amounts of alumina and loss on ignition (LOI), which are deleterious constituents in both the pelletizing as well as iron making processes. Iron ore fines utilized in pellet making consist of alumina in the range of 3.20–3.35% and LOI in the range of 3.50–3.70%. Detailed palletization studies have Optimization of Pellet Plant Straight Grate Induration
احصل على السعر
Iron Ore Pelletizing Process: An Overview IntechOpen
The quality requirements of pellet, such as physical, chemical and metallurgical specifications, depend on each ironmaking furnace and thoserequirements influence the operation ofthe iron ore pelletizing plant. The idea of rolling moist fine ore in a drum to form balls and then drying and firing it was firstEnsure your plant’s high performance and profitability while lowering investment and operating costs with our agglomeration technologies. Our innovative sintering and pelletizing solutions are based on over 60 years’ experience and world-class R&D. TON Traveling Grate Sintering is suitable for sintering a wide range of raw materials, including iron, Sintering and Pelletizing TON
احصل على السعر
Iron ore pellets as a solution to steel—making raw Springer
The beneficiation plant will be connected by a 230-km underground slurry pipeline to a 4.5 Mt/a pellet plant under construction at Kalinga Nagar in the district of Jajpur, close to both industrial development and port facilities, where the ore slurry will be balled and fired into pellets, the highest grade iron ore product used in steel production.TON's traveling grate pelletizing plant is the industry's leading induration technology for iron ore pellet production for a wide range of plant capacities. Based on over 60 years' experience and world-class R&D, our process produces uniform pellets and ensures high performance and quality, with low investment and operating costs, as well asTraveling Grate Pelletizing Plant TON
احصل على السعر
(PDF) Iron ore pelletization ResearchGate
Arrium Australia 0.810 0.810 0.440. 440 Iron Ore. The pelletizing process involves the preparation of ra w materials; the proportioning. and mixing of raw materials; the formation, preheating, andThe raw materials for an integrated steelworks can be classified into four categories, which are iron ores, fluxes, fuels, and reverts. The characteristics of these raw materials strongly affect the metallurgical properties of iron ore sinter and sinter plant performance. An optimal ore blend design is therefore essential to produce low costSinter Plant Operations: Raw Materials SpringerLink
احصل على السعر
Iron Ore Pelletization Technology and its Environmental
remaining is exported. the bulk (around90%) of the iron ore fines get exported,as they cannot by utilised in iron making without agglomeration [3]. As the demand of iron ore is increasing, it is necessary to recover the resources from the mines wastes or lean-grade iron ore through beneficiation. In that case the feed to sinter or A full-scale plant trial of the substitution of a specific organic binder for bentonite was conducted in the company's straight grate pellet plant in Quebec, which produces 9.3 Mtpa of pellets, 36% of which are used as feedstock for the DR process. The results of the full-scale pellet plant trial are given in Table 15.13.Iron ore pelletization ScienceDirect
احصل على السعر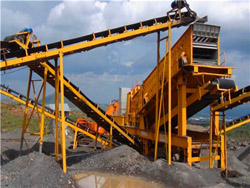
Effects of Pellet Basicity on the Simulated Deposit Formation
Deposit formation in the coal-fired rotary kiln is frequently found in the production of fluxed iron ore pellets by the grate-kiln process and affects normal production. In this paper, the effects of pellet basicity (CaO/SiO2 mass ratio) on the simulated deposit formation were investigated. The results show that the porosity of deposits samples increases from 30.8 The three common processes used in iron ore pellet production are the shaft furnace process, the straight grate process, and the grate-kiln process. 8 As the dominant process for iron ore pellet production in China, the proportion of iron ore pellets produced by the grate-kiln process has exceeded 70%. 9 Deposit formation in a rotary Effects of Pellet Basicity on the Simulated Deposit Formation
احصل على السعر
(PDF) GUIDELINES FOR SELECTING PELLET PLANT TECHNOLOGY
Additional iron ore pellet feed production tha t must be pelletized, 2011-2025. ( 1) As much as 400 Mtpa of new concentrate is forecast to come into production by 2020Ferrexpo and TON Outotec have a long history of collaboration. TON Outotec’s predecessor, Allis Chalmers, delivered the first two grate kiln (GK) pelletizing plants to the Poltava mine in 1976. The plants, with a rated capacity of 3 Mtpy, included a so-termed traveling grate for drying and preheating green ball iron ore pellets, a rotarySuccessful modernization of two grate kiln pellet plants at
احصل على السعر
Iron Ore Pellets and Pelletizing Processes PDF Scribd
Iron ore pellets and Pelletizing processes. Pelletizing is a process that involves mixing very finely ground particles of iron ore fines of size less than 200 mesh with additives like bentonite and then shaping them into oval/spherical lumps of 8-16 mm in diameter by a pelletizer and hardening the balls by firing with a fuel. It is the process of Iron ore pellet reduction experiments were performed with pure hydrogen (H2) and mixtures with carbon monoxide (CO) at different ratios. For direct reduction processes that switch dynamically between reformed natural gas and hydrogen as the reductant, it is important to understand the effects of the transition on the oxide reduction Modeling Isothermal Reduction of Iron Ore Pellet Using
احصل على السعر
(PDF) Development and Evaluation of a Furnace for Lab-scale Pellet
Effect of iron ore mineral and induration temperature on CCS of pellets [2]. Firing curves of tests performed the same day with thermocouple within the sample bed. (HR: average Heating Rate).Gasification equipment was studied for a pelletizing plant with annual production capacity of 8.4 million tons of pellets/year and thermal consumption of 206.1 kcal/kg of pellet. The objective of that study was preliminarily to evaluate the partial replacement of the natural gas injected into an indurating pelletizing machine by Assessment of iron ore pellets production using two charcoals
احصل على السعر
Pelletizing Plants BOLLFILTER
Pelletizing is the process through which iron ore fines are transformed into an agglomerated form called “iron ore pellets” suitable for use in an iron-making furnace at a steel mill, such as a blast furnace or electric arc furnace. In its end product form, a typical iron ore pellet is roughly spherical in shape, measuring from 6 mm to 16
احصل على السعر